OVERVIEW
Kolar Gold Fields (KGF) is located about 100 Kms from Bangalore. It is the biggest manufacturing plant of BEML and was established in 1968. It caters to Design & Development, Manufacturing, Testing and After-Sales-Service of Earth Moving Equipment and its aggregates. The Complex is accredited with ISO 9001 : 2015 for QMS and ISO 14001 : 2015 for EMS by Bureau Veritas (India) Private Limited. The Complex is spread over 2980 acres of land well connected by roads and rail sidings enabling easy transport of heavy equipment & structures through special rake, trailers etc.
The Complex manufactures equipment and aggregates catering to Mining & Construction and Defence Sector. The Complex is equipped with one of the best R&D Centres in Asia with modern infrastructural and testing facilities.
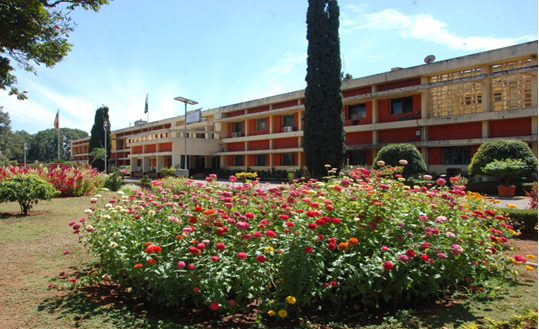
The Division has one of the biggest Machine Shops in Asia housing machine tools of different types and varieties with dedicated product lines, Gear Shop, Fabrication Shops with latest welding facilities including Robotic, Plate Preparation Shop and an exclusive Heavy Equipment Shop to handle major fabrication of structures weighing up to 100 T.
Machining Facilities
- Different Varieties of
- CNC Horizontal Machining Centers.
- CNC Turning Centers.
- CNC Vertical Turret Lathes.
- CNC Milling Machines.
- CNC Heavy Duty Boring Machines.
- CNC Cylindrical Grinding Machines.
- CNC Universal Grinding Machine.
- CNC Wire Cut EDM.
- Heavy Duty Boring Machines ( SKODA, WMW and GLF )
- Heavy Duty Plano Millers.
- Vertical Turning Lathes
- Radial Milling Machines.
- Surface Grinding.
- Internal Grinding.
- Cutting Machines.
The above mentioned machines and machining activities are spread across Machine Shop-I, Machine Shop-II and Machine Shop III. These machines are arranged in all combination of layouts catering to process type and product type in order to achieve maximum output efficiency.
Gear Manufacturing Facilities
- CNC Hobbing.
- CNC Shaping.
- CNC Gear Grinding .
- CNC Gear Shaving .
- CNC Gear Cutter Grinder
- Vertical Broaching.
- Horizontal Broaching.
State-of-the-Art CNC Gear Grinding Machine from Hoffler Germany is installed in the Shop and it has added new dimension to the Gear manufacturing capabilities of EM Division. Gear Shop also houses a Metrology Laboratory wherein Gear Testers of various make including the latest CNC Profile Helix Gear Tester from Wenzel, Germany are available.
Heavy Equipment Shop
- Heavy Duty Press Brake 1250 T
- Heavy Duty Centre Lathe
- SKODA Heavy Boring Machine Horizontal
- Radial Drilling Heavy Duty
- Material handling facilities
Plate Working & Fabrication Facilities
- CNC Flame Cutting Machines
- CNC Plasma Cutting Machines.
- Plate Beveling.
- Plate Shearing.
- Rolling and Straightening Machines
- Hydraulic Presses & Press Brake.
- Shot Blasting Machines.
- Heavy Duty Plano Milling Machines
Fabrication activities are spread over 4 shops, viz., Fabrication Shop, Dozer Fabrication Shop, Minor Fabrication Shop and Heavy Equipment Shop. The Following types of welding is carried out in the shops.
- GMAW – Gas Metal Arc Welding
- FCAW – Flux Cored Arc Welding
- GTAW – Gas Tungsten Arc Welding
- SAW – Submerged Arc Welding
- SMAW – Shield Metal Arc Welding
This facility has also got a separate Pipe Manufacturing Unit with NC Pipe Bending Machines and different welding process including TIG.
Heat Treatment
Furnaces:
- Sealed Quench Carburising Furnaces.
- Carbo Nitriding Furnace
- Spray Quenching
- Low Tempering / High Tempering Furnaces.
- Gleason Press Unit.
- Controlled Atmospheric Furnace.
- Nitriding Furnace.
Induction Hardening Machines
- Single Shot IH Machine for all heavy Duty Gears.
- Tooth by Tooth Induction Hardening Machine.
- Radial Frequency Induction Hardening
- PLC Controlled Induction Hardening Machines for Track links
- CNC Vertical Shaft IH Machine.
- Roller Hardening Machine.
- Roller Shaft hardening Machine.
Compressors
Ten Nos of 500 CFM and 2 Nos. 100 CFM Compressors operating at 6 Bar Pressure are installed in the Division. The generated Pneumatic Pressure is well connected to all the Manufacturing and Assembly Shops through Leak Proof Pipe Line Arrangement.
Hydraulics & Powerline (H&P) Division was established in the year 1987 with an area covering 14.5 acres. This Division is distinctly separated from the Mother Plant (EM Division) considering the classified nature of the products and is located adjacent to R&D Division to manufacture Hydraulic Aggregates, Axles and Transmission Assemblies. The sapling of 1987 has grown now into an independent strategic business unit and a profit center. The division has successfully manufactured high precision components and assemblies indigenously. Currently, the unit is catering to captive requirements and external customers.
The Division is well equipped with highly sophisticated machines and is supported by the R&D Division with CAD / CAE facilities and modern laboratories. The Division has highly skilled labour force working under qualified and experienced supervisory personnel, who constitute the core competence and strength of the division.
H&P Division’s major customers are from industry segments like Coal, Steel, Cement, Defence, Power and Construction Sector.
Products manufactured at H&P Division are:
Hydraulic Aggregates | Powerline Aggregates |
Gear Pumps | Transmissions |
Cylinders | Axles |
Suspensions | Bevel Gears |
Control Valves | Final Drive |
Machining Facilities
- CNC Turning
- CNC Turnmill
- Horizontal Machining
- Honing
- CNC Grinding (Internal & Surface, Cylinder and Gear)
- CNC Boring
- Special Purpose Machines
- Conventional Machines
Gear Manufacturing Facilities
- Gear Hobber
- Spline Hobber
- Gear Shaper
- Gear Shaver
- Gear Grinding
- Bevel Gear
- Spiral and Hypoid
Heat Treatment Facilities
- ISO Thermal Annealing
- Normalizing
- High Temper Annealing
- Quenching
- Low Tempering
- Gas Carburizing
- Press Quench (Gleason)
- Nitriding
Test Facilities
- Cylinder Test rig
- Pump Test rig
- Transmission test rig
- Axle Test rig
During the year 2004, BEML Limited through a lease agreement with Bharat Gold Mines Limited (BGML) had taken over the erstwhile Nundyduroog workshop for the purpose of developing the same into a manufacturing unit to supplement the needs of Bangalore complex. The premises consist of Factory workshops and other buildings with a total area covering 22 acres.
BEML constructed three new Hangars viz. Under Frame Hangar and Shell Hangar and Furnishing hangar. The shell hangar consists of 3 assembly lines. Two coach Traversers (50T & 100T capacity) are available for transferring shells in between the assembly lines. The hangars are equipped with two numbers of each 10 T and 20 T EOT cranes. Furnishing hangar is constructed in the year 2009 for fully furnishing of Rail coaches and delivered GS/GSCN Rail coaches during 2010 onwards to Indian railways. The initial capacity of hangars is to fabricate around 80 Rail coach shells per annum. The Division is accredited with ISO 9001 – 2015 Certificate for QMS by BVCI.
Division is equipped with the following facilities:
- CNC Flame Cutting Machines.
- CNC guided Plasma Cutting Machines.
- Plate Shearing machines.
- Rolling and Straightening Machines
- Press Brakes.
- Grit Blasting Machines.
- Foil Roll welding machines.
Fabrication activities are carried out on shop floor. The Following types of welding are carried out:-
- GMAW(MIG) – Gas Metal Arc Welding
- SAW – Submerged Arc Welding
- SMAW(ARC) – Shield Metal Arc Welding
The Unit has facilities for Grit Blasting ,Painting and Roof water leak testing of Rail coaches.
Air Compressors and DG sets
The division is equipped with AIR COMPRESSORS – 800CFM/300/100 to cater the needs of production.
The division is equipped with self sufficient captive power DG SETS of following capacities.
D.G SET – 500 KVA
D.G SET – 360 KVA
Facilities
The Unit has the facilities to fabricate/produce the products depicted below:
- Non Metro Rail coaches, E.M.U’s and Rail Maintenance vehicles.
- BOMN Wagons
- BFAT Wagons
- BRSTN Wagons
- Passenger Boarding Bridges (PBB)
- Rail Grinding Machines (RGM)
During the year 2004, BEML Limited through a lease agreement with Bharat Gold Mines Limited (BGML) had taken over the erstwhile Central Workshop (Mechanical) for the purpose of developing the same into a manufacturing unit, under the concept of SBU. The premises consist of factory workshops and other buildings with the total area of about 36 acres.
BEML has engaged ex-BGML employees and their children with requisite qualifications and experience for manufacture/fabrication of Railway components / sub-assemblies.
The Unit has five hangers with four hangers for fabrication activities and one hanger for machining activities. The fabrication hangers are equipped with required overhead cranes for material handling and sufficient welding machines.
This Unit is in-line with the requirements of Earth Moving Division and Hydraulics & Powerline Division.
The Unit is presently manufacturing the parts depicted below:
Fabrication
- Structures for Excavators
- Structures for Loaders
- Structures for Defence Equipment
- Structures for Underground Mining Equipment
Machining
- Dozer Castings
- Under Carriage Items
- Aggregates for Hydraulic Shop
- In-House Structure Details
OVERVIEW
BEML Limited (formerly known as Bharat Earth Movers Limited) as a full-fledged corporation was established in 1964 with Bangalore Complex as the mother unit.
The Bangalore Complex (the then Rail Coach Factory) was in existence from 1947 as a part of Aircraft Factory (currently Hindustan Aeronautics Limited). Initially, the division was manufacturing Rolling Stock producing various models of Broad Gauge Coaches.
Subsequently, over the years, the metro coaches and some of the defence products manufacture also has been added in this complex.
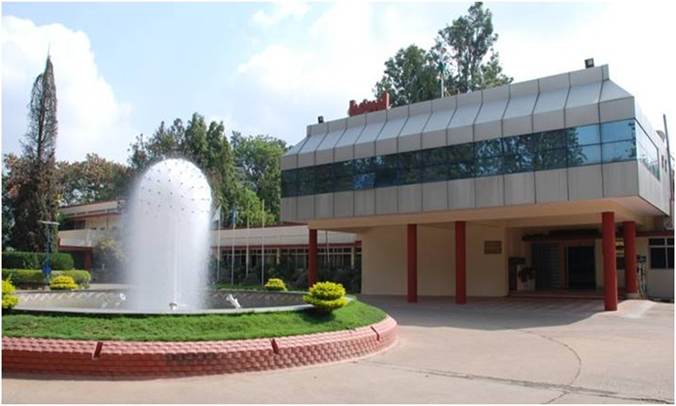
Manufacturing Facilities
The complex has large sophisticated machines such as CNC Turning Center, CNC Boring machines, Vertical Turret lathes and Honing machines in addition to General purpose machines. The dedicated machines are:
- 248 M Test track for Metro and AC-EMU testing
- Bogie testing machine up to 60 Ton capacity
- Well-established metrological laboratory for Quality products
- Well-laid Railway lines inside the production shops for smooth stage production
- Railway sidings for delivery of coaches and receipt of raw materials
- Boring machines for Axle box
- AF / Axle Box spring seat machining
- Wotan internal grinding machine for Axle box
- Vertical turret lathe for Axle box machining
- Honing machine
- Flash butt welding machine for Brake Tension rod
- Hydraulic press 100 T for Bush pressing
- Laser cutting machine
- NC shearing machine
- Punch press: 40 – 1000 T
- Press Brake: 40 – 500T
- Optical tracer flame cutting machines
- CNC Flame cutting machine
- Shot blasting machine for (Rolled section & Plates)
- Shearing M/C to 30 mm capacity with inbuilt Beveling for weld joints
- Spot welding machine
- Shot blasting machine (Rotary & conveyor type)
- Foil Roll welding machine for welding of corrugated sheets used for Floor
- Corrugated rolling machine
- Plasma Cutting machine
- Submerged Arc welding sets
- Check & straightening machine for Bogie components
- Robot Spot Welding Machine
- Roller bending machine for roof skins
- Foil Roll-Welding M/C for Roof, Side wall & End wall of Rail coaches
- Roof leak test facility
- Conveyorised painting booth
- Shot Blasting facilities for Rolled Sections and plates
- Lifting jacks of 16 T capacity
- Air brake testing equipments (4 numbers)
- Traversors of 75 T capacity (2 numbers)
- Water leak test facility for Metro cars
OVERVIEW
BEML Limited, the trusted name for over 52 years in mining and construction industry, channels its expertise into the priority sector of energy with the manufacture of fuel-efficient diesel engines. Established in the year 1991 in Mysuru, with technical know-how from Komatsu Japan, BEML diesel engines are built for maximum reliability, high performance and lasting value. These engines are backed by the facility of application engineering, multi-location sales & service network and rehabilitation facility.
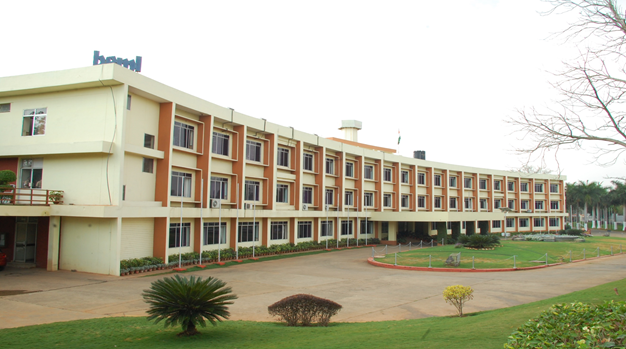
Some of the major facilities of the division are –
- Welding Robot – to carry out accurate and continuous welding of major structures of Dumpers.
- CNC Flame cutting machines, Hydraulic Press brakes – to cut & bend Steel plates to meet manufacturing requirements.
- Spinner Jigs – to carry out full welding of Frames
- Shot blasting facility – to perform shot-blasting operations on fabricated structures to provide good surface finish and make it free from rust.
- CNC Boring machines – for accurate machining of big structures like Axle structures.
- Roof top 100 kWp On-grid Solar PV Power Plant
Engine Division manufactures heavy duty Diesel Engines for application on a wide variety of Earth Moving, Mining and Construction Machinery and Defence Equipment. Apart from these, the engines are also offered for other industrial applications as well as diesel generator sets. BEML Engines are used on Bull Dozers, Dump Trucks, Motor Graders, Wheel Loaders, Pipe Layers, Hydraulic Excavators, Loading Shovels, C Crane, Aircraft Towing Tractors, Backhoe Loaders, Water Sprinklers and Heavy Duty Trucks. These Engines are capable of operations over a wide terrain right from sea level conditions to high altitude (19,000ft) as well as under sub-zero conditions.
In-House Manufacturing Facilities
A. Machine Shop:
Machine shop consists of state-of-the-art technology dedicated machines for manufacture of following Engine components
- Camshaft Line
- Connecting Rod Line
- Engine Block Line
- Flywheel Housing , Gear Case & Front Cover Line
- Engine Cylinder Head Line
- Flywheel balancing machine
B. Engine Assembly:
- Four Assembly Lines
- Spinner Jigs & Turn Tables
- Single Spindle, Twin Spindle Electric Nut Runner
- Ultrasonic Cleaning facility
- Nitrogen Chilling Facility
- FIP Calibration Set Up
- Injector Nozzle Tester
C. Engine Testing
- SCHENCK Hydraulic Dynamometer ( 1200 kW- 2 Nos , 900 kW)
- ZOLLNER Hydraulic Dynamometer (660 kW)
- SAJ FROUDE Hydraulic Dynamometer (750 kW- 2 Nos)
- SAJ TEST PLANT Eddy Current Dynamometer ( 400 kW and 720 kW)
- Exhaust gas emission test facilities for CO, NOx, HC, PM & Smoke
D. Engine Painting
- Down Draught Water Wash Spray Paint Booth
High Technology Machining Facilities
- Flexible Manufacturing System (FMS) (1250 x 1250 mm Pallet Size)
- Multi pallet Horizontal Machining Center (1250 x 1000 mm Pallet Size)
- Crank and CAM Bore SPM
- Cam profile milling machine
- CNC Camshaft Grinding Machine
- Auto Straightening Press
- Connecting Rod Weighing and Balancing SPM
- Honing Machine
- CNC Horizontal and Vertical Machining Centers.
- CNC Valve Seat and Valve Guide Generating SPM
Inspection Technologies
- Three Co-ordinate Measuring Machine
- Computerized automatic Cylinder Head Pressure Leak Testing Machine
- Industrial Endoscopy for internal passage analysis
Special Processes
- Shot Peening
- Induction Hardening and Tempering
Metrology and Gauge Calibration
Metrology Lab is NABL accredited.
Facilities at Material Testing and Metrology Lab
|
|
Renewable Energy Projects
- Roof top 100 kWp On-grid Solar PV Power Plant
OVERVIEW
The green field project at Palakkad, Kerala was put on stream on 16th May 2010, in record time of less than 6 months with an outlay of Rs 260 crore.
The plant was set up to cater to the requirements of Defence Ministry & Indian Railways. Since inauguration the Palakkad complex has supplied 150 Rail coach Shells and Bogie Frames and 500 HMV Trucks.
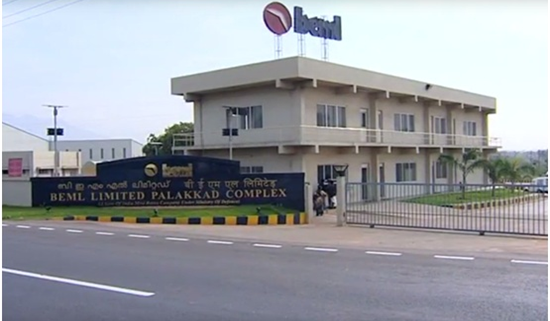
- BEML – HMV Trucks 12×12, 10×10, 8×8, 6×6, 4×4 & Variants
- Ground Support Vehicles for Guided Missile Programme
- Heavy, Medium and Light Recovery Vehicles
- 50T Trailer for Tank Transportation
- Mil Rail Coaches and Mil Wagons
- GS & GSCN Coaches for Indian Railways
- Bogie Frames for conventional & EMU Coaches
- Aggregates for AC EMU & DEMU Coaches